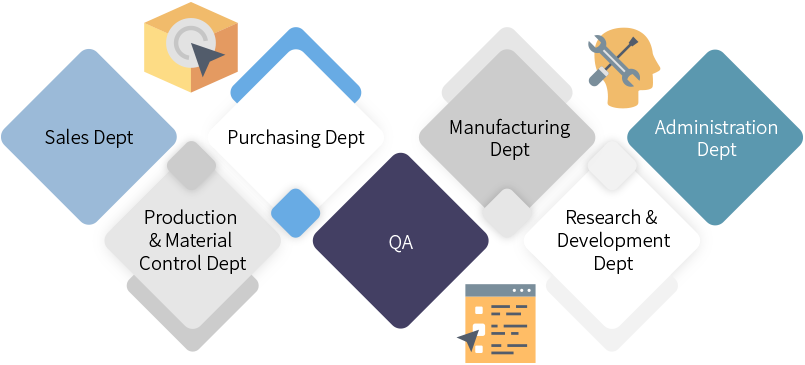
Fully participation
Customer demand oriented:Sales/Research and Development/Production & Material Control/Manufacturing/Quality assurance/Purchasing department
Fully throughout
Customer demand passthrough from all departments to all stages Development stage→Trial run stage→Mass product stage→Marketing feedback stage
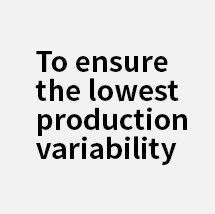
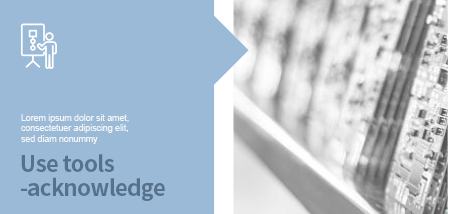
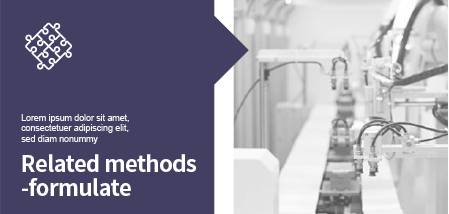
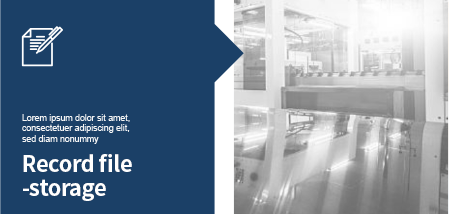
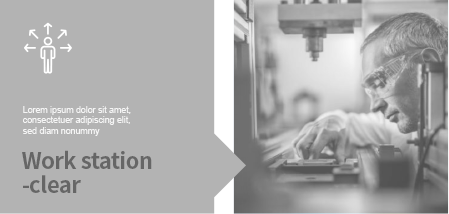
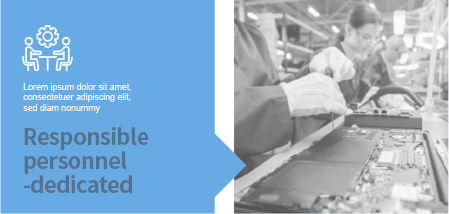
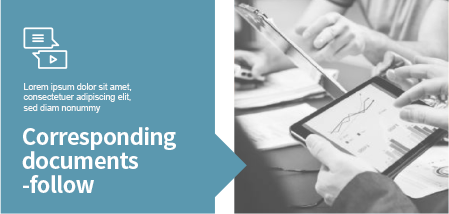
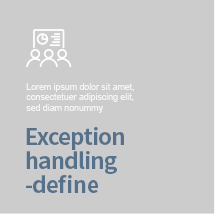
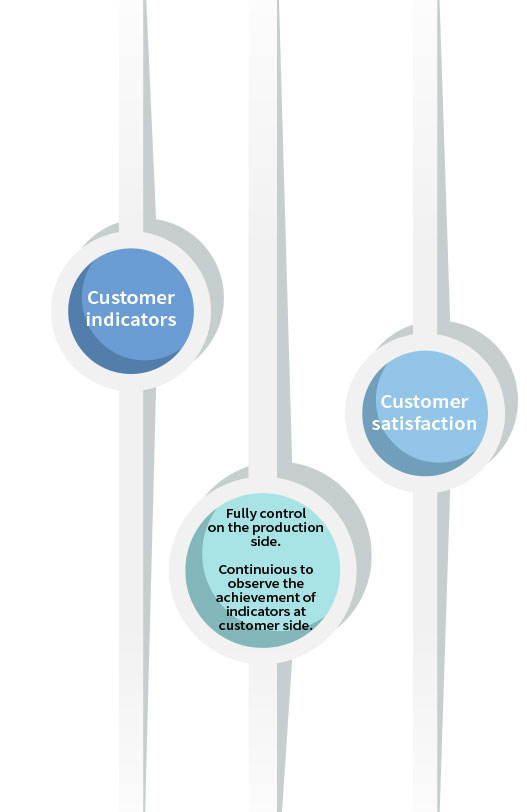
Fully control on the production side.
Continuious to observe the achievement of indicators at customer side.
Plan for the process of implementing measurement, supervision, analysis and improvement to ensure the quality records and quality activities related data that occur during the production process,these data can be executed various analysis to discover the potential problems and trends, using data analysis to prevent issue occur from production line to improve customer satisfaction.
In order to achieve the goal of perfection, the following reaction procedures has clearly defined:
- Implementation requirements and regulations for incoming material inspection, process inspection, and finished product inspection procedures
- Internal quality audit implementation procedures
- The essentials of applying to quality control method to statistical techniques
- Corrective and preventive action procedures
- Customer satisfaction evaluation procedures
- Customer complaint handling procedures
- Non-conforming product handling procedures
- Customer return processing procedures
- Continuous improvement control procedures
- Special use(waive) management procedures
IQC using AQL standard(MIL-STD-105E-II) to ensure the quality of incoming material.
From the raw material to finished goods, Hamburg has executing the Total Quality Control system to ensure
each process are all under control
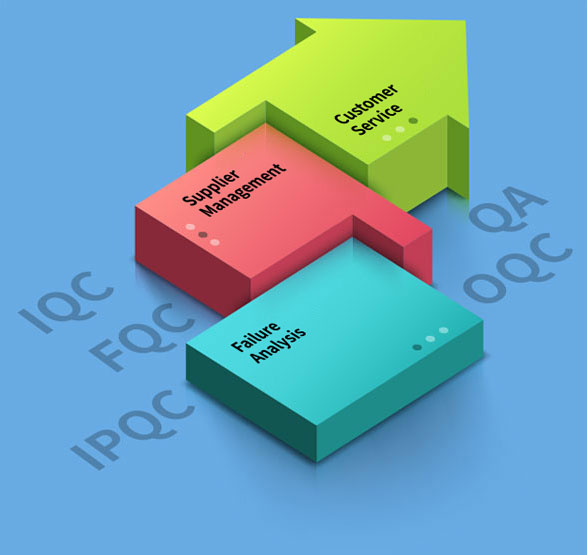